Hey all,
Here it is, the project thread for my Ibanez RG570!
I picked this axe up for a very good price from a fellow GFSA member as I'd been looking for a shred machine for a while and was on a bit of a budget. It needed a lot of attention, the finish was badly chipped and dinged, the pickups had been removed and the frets were very, very worn, so I decided to turn it into my first project (bit of a risky move in retrospect; even though I paid very little for the axe, it plays like a dream with that legendary original Wizard neck!).
The plan was to give her a full refret and refinish. I went with Stew-Mac's tallest/widest fretwire for the refret and for the finish, I had the idea to get hold of a very thin maple veneer for a relatively easy yet classy-looking trans finish.
Well, I got a little more than I bargained for; the veneer I ordered from Stew-Mac turned out to in fact be more of a cap, at 7mm in thickness, so with advice from some other forum members (you know who you are, your advice has been and continues to be invaluable, THANK YOU!!), I decided that the only way yo go would be to create a "drop-top"; taking the basswood body down by about 5mm to accommodate the maple top and steaming-bending the maple to fit the arm contour on the top of the guitar.
Here are some pics, apologies for the poor quality, I used my phone to take these.
Here is what the guitar looked like before I got started:
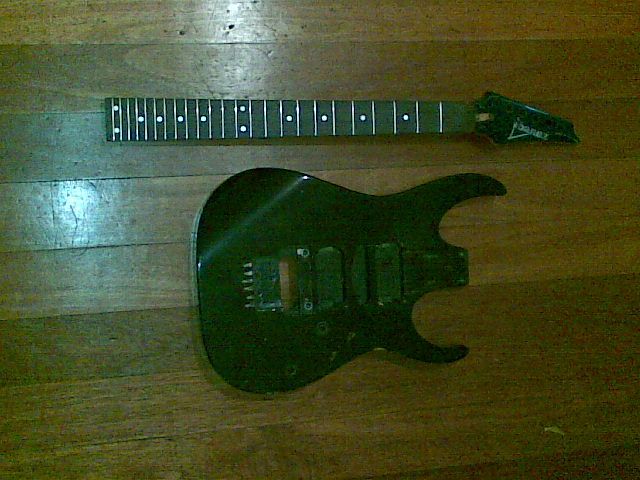
Removing the old frets using my modified end nippers (ground flush on the end) and a soldering iron. It looks worse than it actually is because the fretboard was really dirty. I managed to get minimal chipping of the rosewood:
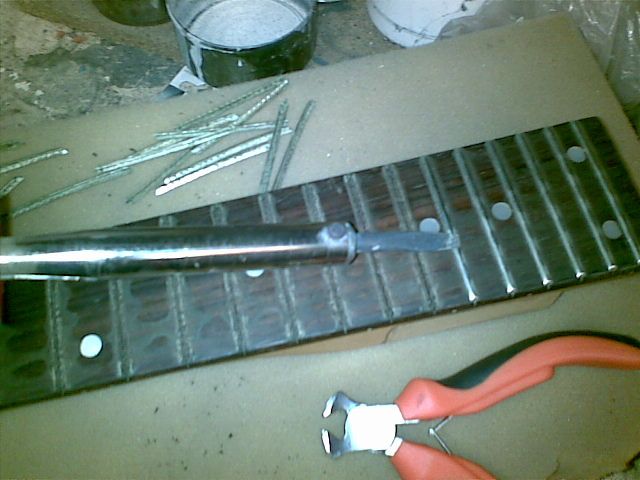
Levelling the fingerboard using a heavy steel sanding beam and 220 grit paper. I then used a radius sanding block (16") with 220 through 600 grit paper:
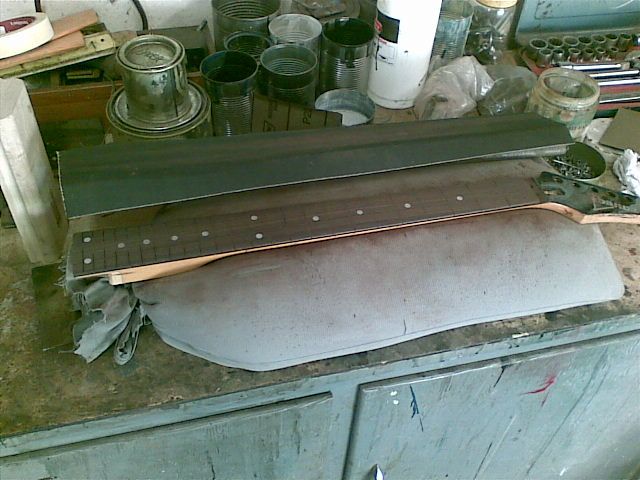
New frets installed, still need polishing though. Some of the frets could have seated better but I chalk that down to not bending them properly before installing. All in all not too bad for a first-timer though, but a nerve-wracking experience!
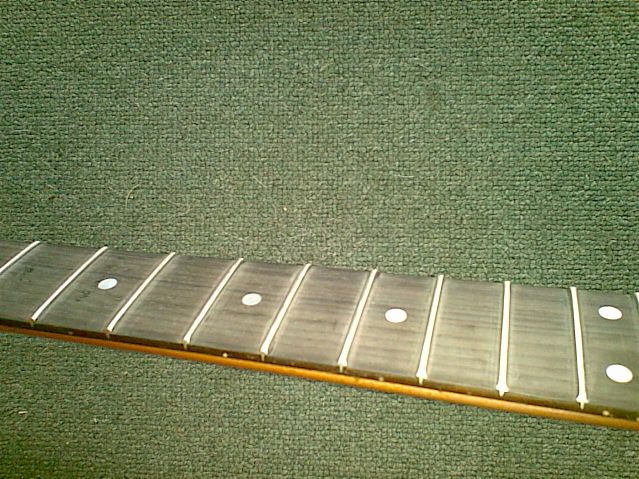
TO BE CONTINUED.....
Here it is, the project thread for my Ibanez RG570!
I picked this axe up for a very good price from a fellow GFSA member as I'd been looking for a shred machine for a while and was on a bit of a budget. It needed a lot of attention, the finish was badly chipped and dinged, the pickups had been removed and the frets were very, very worn, so I decided to turn it into my first project (bit of a risky move in retrospect; even though I paid very little for the axe, it plays like a dream with that legendary original Wizard neck!).
The plan was to give her a full refret and refinish. I went with Stew-Mac's tallest/widest fretwire for the refret and for the finish, I had the idea to get hold of a very thin maple veneer for a relatively easy yet classy-looking trans finish.
Well, I got a little more than I bargained for; the veneer I ordered from Stew-Mac turned out to in fact be more of a cap, at 7mm in thickness, so with advice from some other forum members (you know who you are, your advice has been and continues to be invaluable, THANK YOU!!), I decided that the only way yo go would be to create a "drop-top"; taking the basswood body down by about 5mm to accommodate the maple top and steaming-bending the maple to fit the arm contour on the top of the guitar.
Here are some pics, apologies for the poor quality, I used my phone to take these.
Here is what the guitar looked like before I got started:
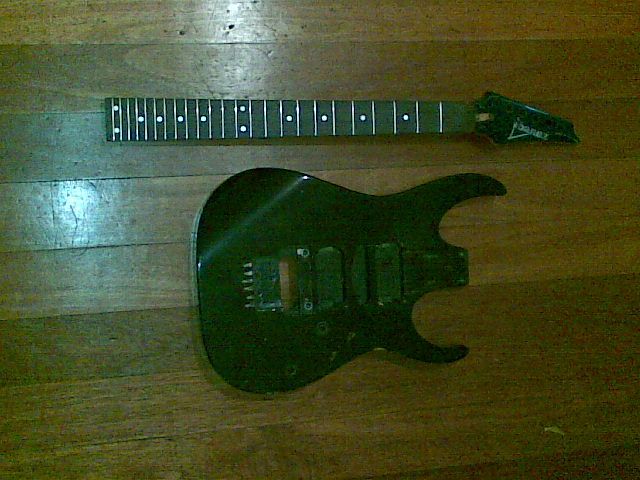
Removing the old frets using my modified end nippers (ground flush on the end) and a soldering iron. It looks worse than it actually is because the fretboard was really dirty. I managed to get minimal chipping of the rosewood:
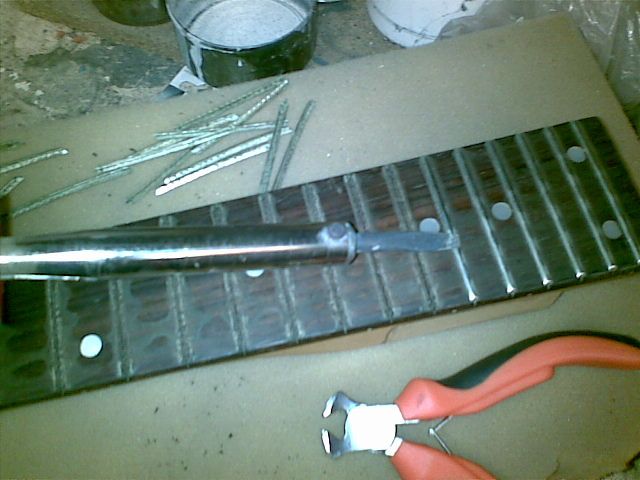
Levelling the fingerboard using a heavy steel sanding beam and 220 grit paper. I then used a radius sanding block (16") with 220 through 600 grit paper:
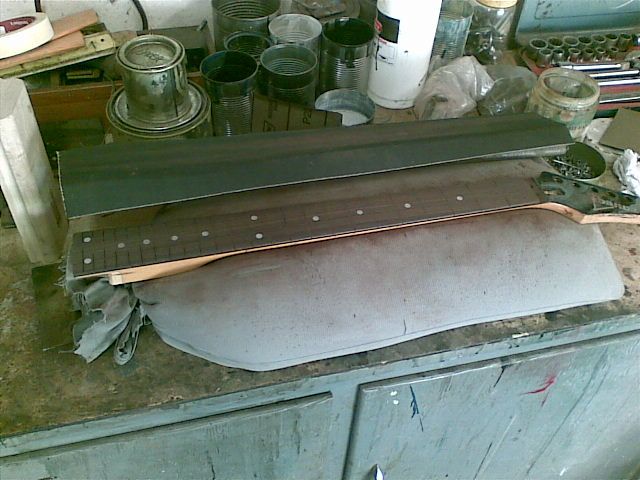
New frets installed, still need polishing though. Some of the frets could have seated better but I chalk that down to not bending them properly before installing. All in all not too bad for a first-timer though, but a nerve-wracking experience!
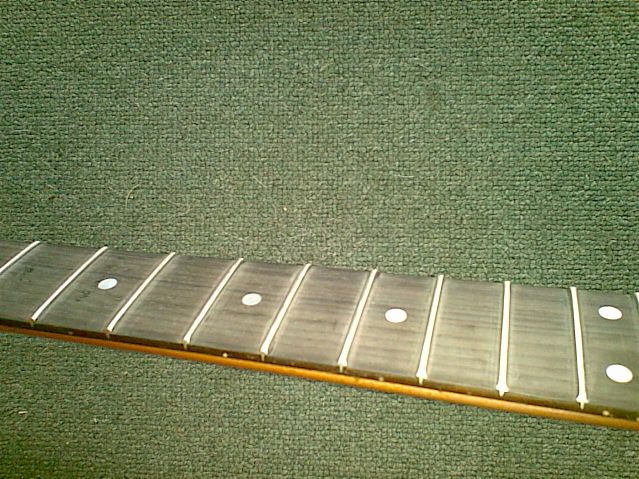
TO BE CONTINUED.....