Alright, after receiving some great advice in this thread (http://www.guitarforum.co.za/setup-mods-and-repair/building-a-guitar-case-some-ideas), I've decided to get to it and start building this thang. Huge thanks must go out to all who offered advice in the other thread and especially to Neon Gecko who e-mailed me some very good advice accompanied by detailed descriptions and drawings.
As promised, here are some pics documenting the process. It has to be mentioned from the outset though that I am by no means an expert and I will make plenty of mistakes and probably do a number of things twice or more times. In the end I decided that this was that excuse I needed to buy the router I've always wanted. Similar results would probably have been attainable by simply using a jigsaw but I figured that I'd like to get the four cuts exactly the same and the router was just perfect for that.
So step 1 was to print the design so that it can be cut from a piece of supawood for the routing jig. Here is the image of the design. The blue section is the shape of the base and top of the guitar case. The black line is what I printed and is a line 8mm from the outer edge of the desired shape. I measured the distance from the router's guiding flange to the cutting edge of the bit as 8mm and so printed a line 8mm inside the desired cutting line.
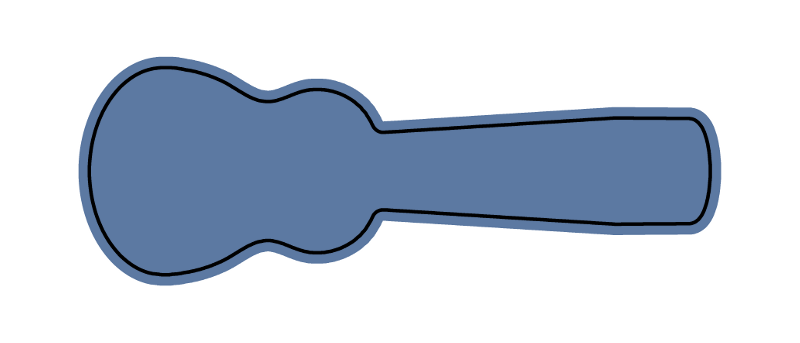
Here is where I made my first mistake. I measured the size of the Ukulele and figured that 1.5cm extra all around should be enough for the plush padding inside the case. The cut was made accordingly and having done it now I'm second guessing that 1.5cm. It might be a rather tight fit. Will have to wait and see.
At any rate, this printout was then glued to a piece of 9mm supawood which would serve as the routing jig.
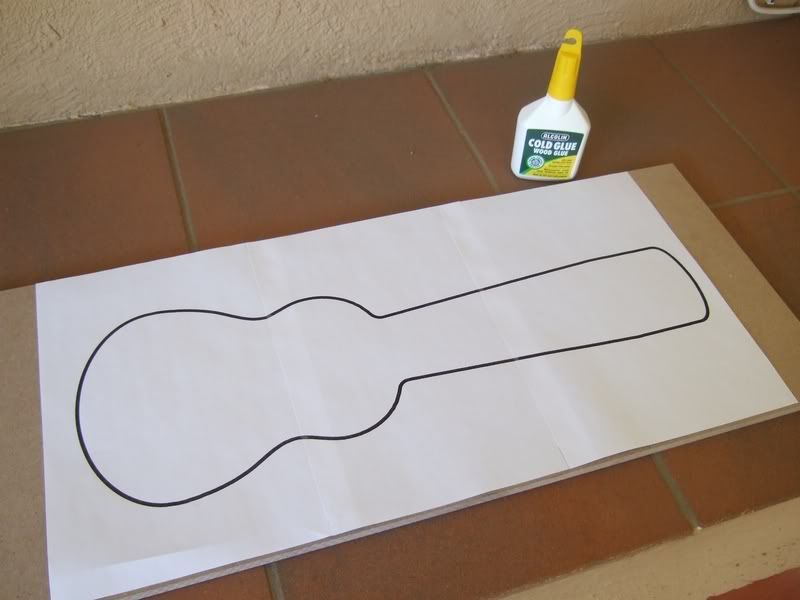
Let's interrupt quickly just to show the bill of materials - at least for the woodworking phase of the project.
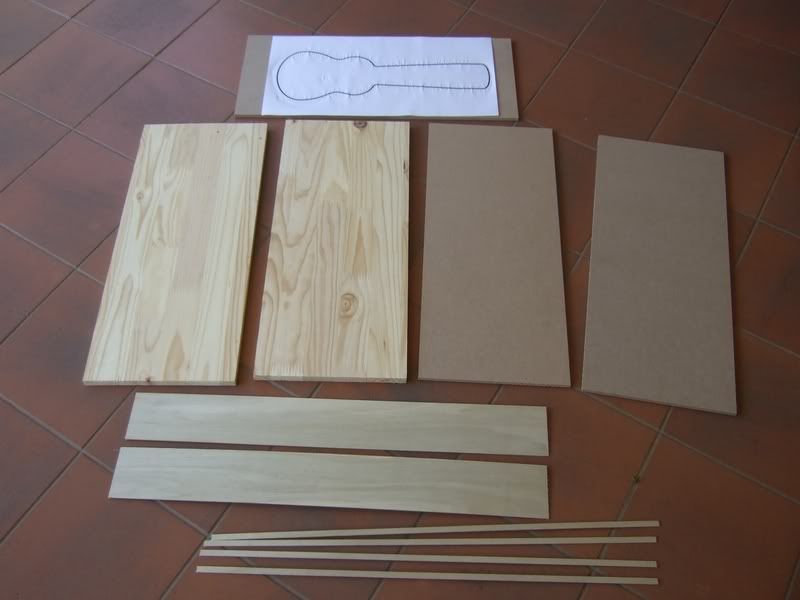
That is:
3 pieces of 9mm supawood, 300x700mm. One to be used for the routing jig and two for the base and top of the case.
2 pieces of 20mm pine, 300x700mm. These will be used as the template to bend the plywood sides.
2 strips of 3mm plywood, 100x800mm. One will be used for the sides of body section of the case and the other on for the neck section.
4 strips of 3mm plywood, 10x800mm. These will be used for the sides of the lid. I think I know how I'm going to do this but it's a vague notion so far and hard to explain. You'll have to wait and see.
OK, so now that the printout is glued onto the supawood, cut it out with a jigsaw.
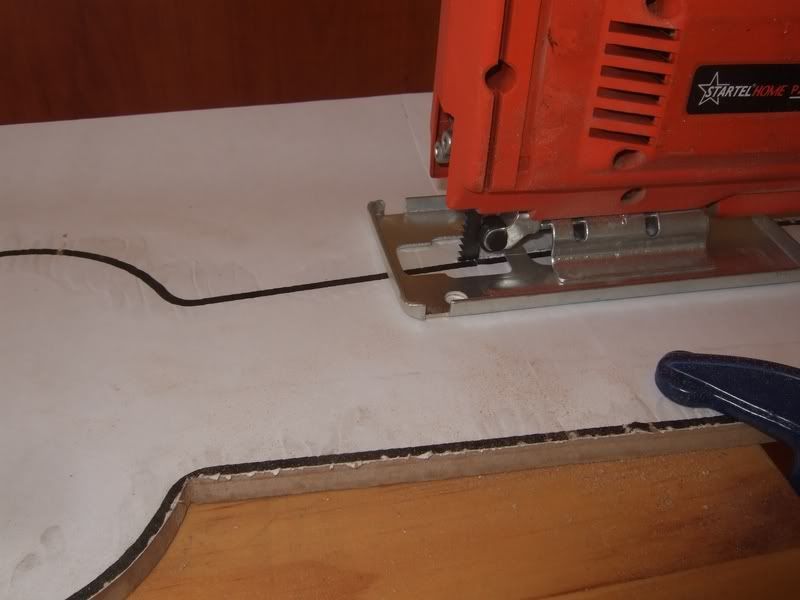
Lessons learned: Rather cut a little bit further from the line. You can always file or sand the wood down to the line but if the jigsaw blade wanders over the line you're pretty much screwed. In Neon Gecko's sage advice: "You can always take wood away but you can never put it back." I was lucky though and only slightly cut into the line in one place. It might not be a big problem but it does bug me a little.
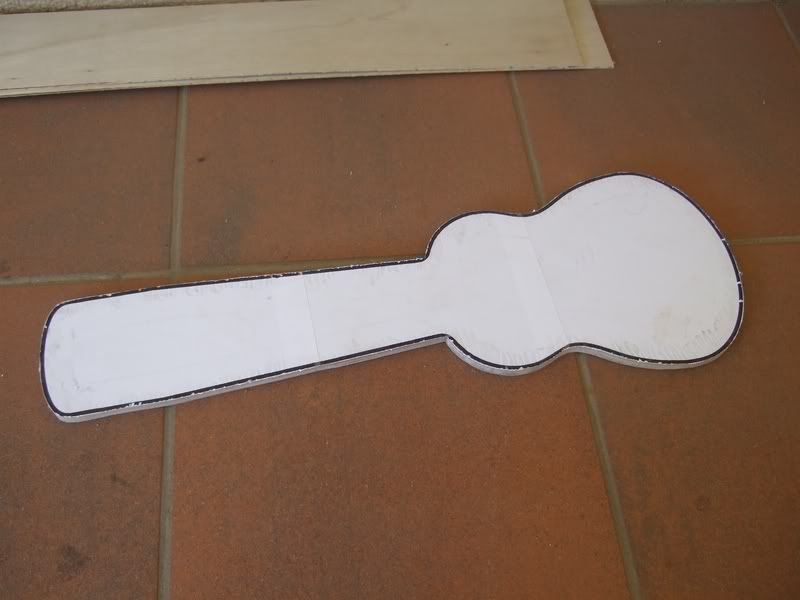
If you look closely, you'll notice that along the side of the neck section, near the tip (in the bottom left of this image) there is a slight concavity to the cut. I didn't even notice this until I started routing around the jig.
OK, so another thing I'd have to make provision for was the fact that my router bit would not be long enough to cut through a 20mm plank of pine. What I did was to sandwich the four planks together and put the template on top, clamp it all together and then drill a few holes through the whole shebang. It is vital that these holes are drilled exactly perpendicular to the planks. A drill press would have been ideal but seeing as I only have a hand held drill I had to eyeball it. I got it fairly accurate but still think I'd have gotten more accurate results using a drill press. The point of drilling these hole is so that I can fit the template to one side of the pine plank, route down to just more than half the thickness of the plank and then fit the template to the back side of the plank and have it line up exactly with the cut made on the front side.
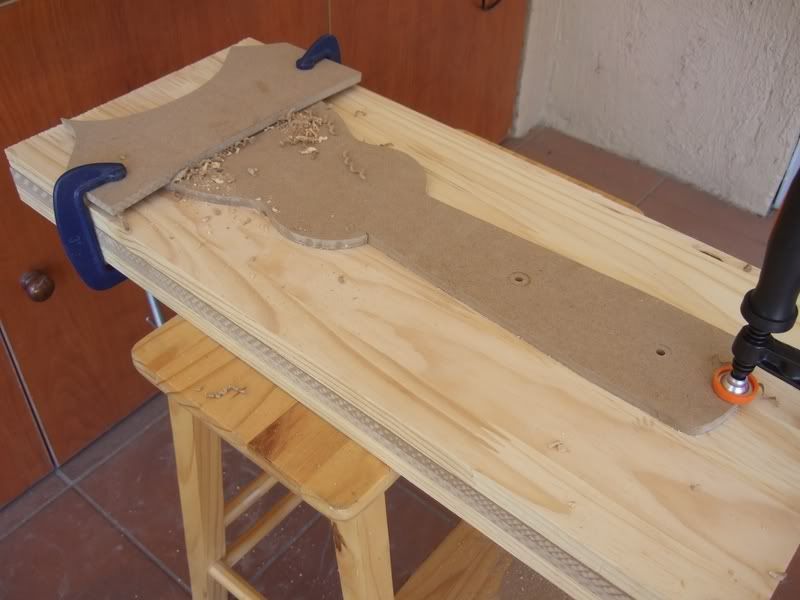
That extra bit of wood on the body side of the template is simply my way of clamping it down. I didn't have clamps that would reach all the way in so I used a piece of off cut supawood and clamped the template down with that.
I then used short dowels of 6mm diameter to fit the template onto the plank to be routed.
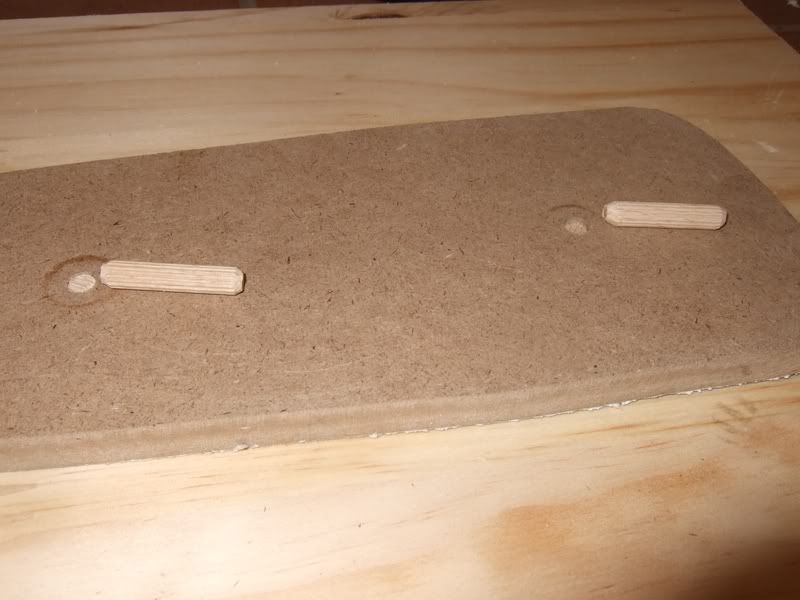
Just important that the dowels don't protrude above the surface of the jig as that would impede the movement of the router sole over the jig.
Now the fun part started. Route along the jig, starting with a shallow cut and progressively cutting deeper. Neon Gecko's rule of thumb seemed to work well that you don't cut deeper than the diameter of the bit. Seeing as I was using a 4mm bit I cut deeper in increments of 4mm.
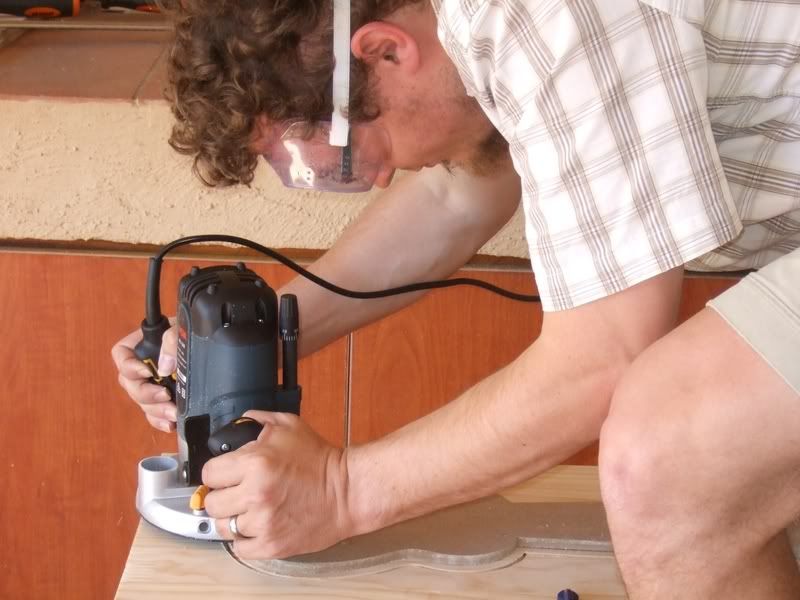
Here is the cut after I reached maximum depth (13mm). After this I flipped the plank around and attached the template again, using the same registration dowels. Notice at the bottom right of the neck section the cut is ever so slightly concave. I'm still hoping this won't affect the end result too badly.
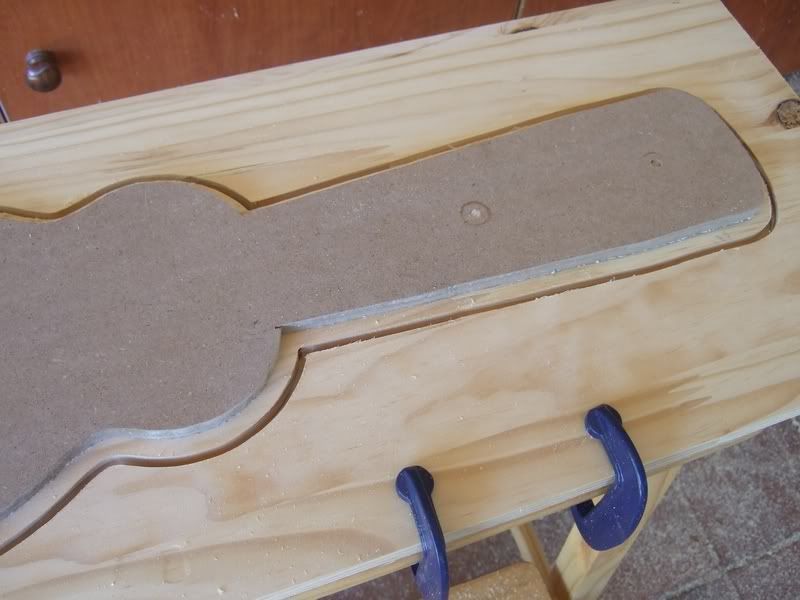
Lesson learned: After finishing a cut, wait for the router to come to a complete standstill before lifting it up. If you don't, you run the risk of breaking your bit. OK, so the whole thing didn't snap in two but I did lose the very tip of the cutting edge which wasn't the biggest disaster but it did mean the the shaft of the bit was now ever so slightly longer than the cutting edge. This meant that consecutive cuts was a bit harder as the shaft would feel the grain of the wood before the cutting edge cuts it. I'll be more careful with future bits but this one did last for all four planks that had to be cut.
Once the cut is made through the plank, rinse and repeat. The second pine plank was cut in exactly the same way and then it was time for the 9mm supawood planks.
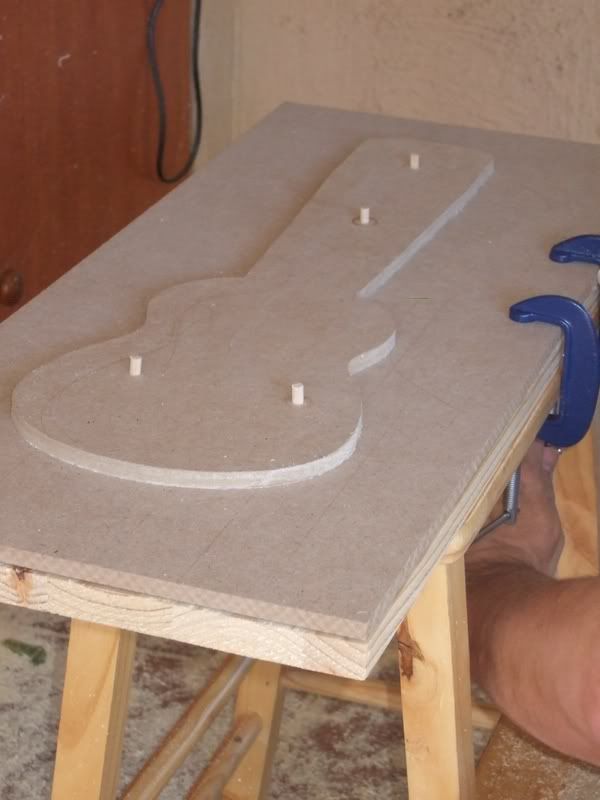
For the two supawood planks the registration holes was probably not required and it would have been more correct, I suppose, to simply clamp the template to the plank and route it without having to drill unsightly holes through the plank. Seeing as the wood will ultimately be covered by vinyl anyway I figured that it wasn't really a problem and I could drill the holes without much reason for concern. Besides, the dowels were a very useful way of fixing the jig to the plank.
And here is the final cut through the 9mm supawood. Of course, it is important to have some other piece of wood underneath the supawood so you don't route into your work surface.
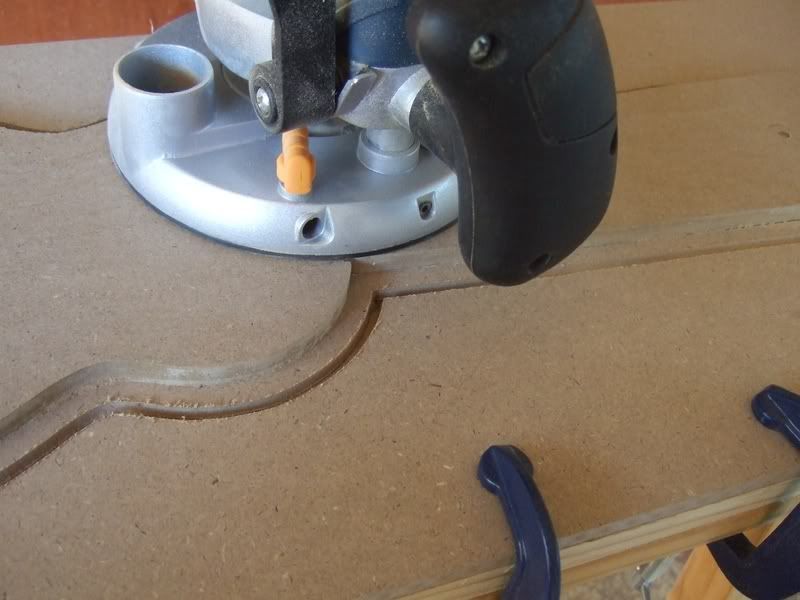
Then, rinse and repeat until you end up with this:
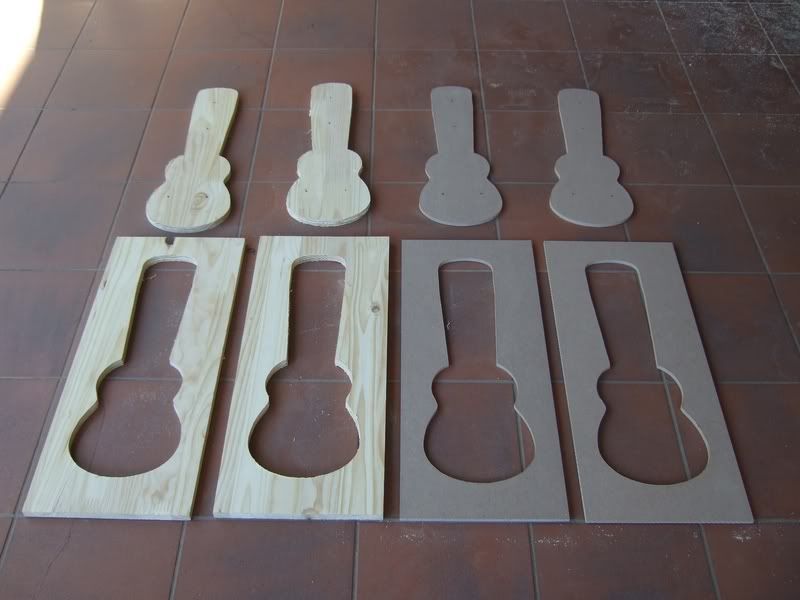
The final step of course is to crack open your hops based beverage of choice as a celebratory libation for making your very first jig-based router cuts. It feels great.
So that's how far I got for now. The next step will be to soak and bend the plywood around these templates. It remains to be seen if the 3mm plywood can actually bend to these curves. I'm particularly concerned about the small curve between the two bulbs of the body but that will have to wait until I get some more time to spend on this.
As promised, here are some pics documenting the process. It has to be mentioned from the outset though that I am by no means an expert and I will make plenty of mistakes and probably do a number of things twice or more times. In the end I decided that this was that excuse I needed to buy the router I've always wanted. Similar results would probably have been attainable by simply using a jigsaw but I figured that I'd like to get the four cuts exactly the same and the router was just perfect for that.
So step 1 was to print the design so that it can be cut from a piece of supawood for the routing jig. Here is the image of the design. The blue section is the shape of the base and top of the guitar case. The black line is what I printed and is a line 8mm from the outer edge of the desired shape. I measured the distance from the router's guiding flange to the cutting edge of the bit as 8mm and so printed a line 8mm inside the desired cutting line.
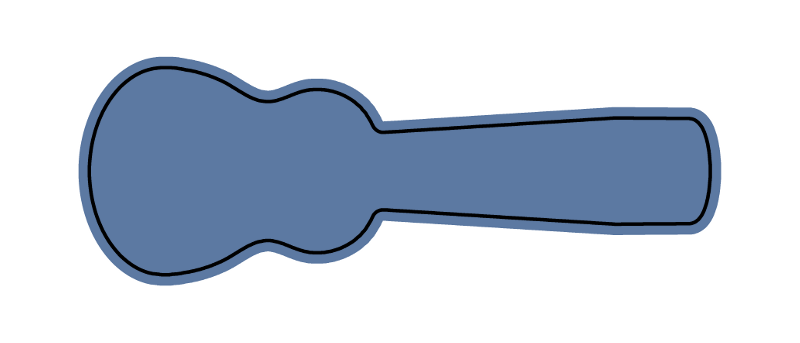
Here is where I made my first mistake. I measured the size of the Ukulele and figured that 1.5cm extra all around should be enough for the plush padding inside the case. The cut was made accordingly and having done it now I'm second guessing that 1.5cm. It might be a rather tight fit. Will have to wait and see.
At any rate, this printout was then glued to a piece of 9mm supawood which would serve as the routing jig.
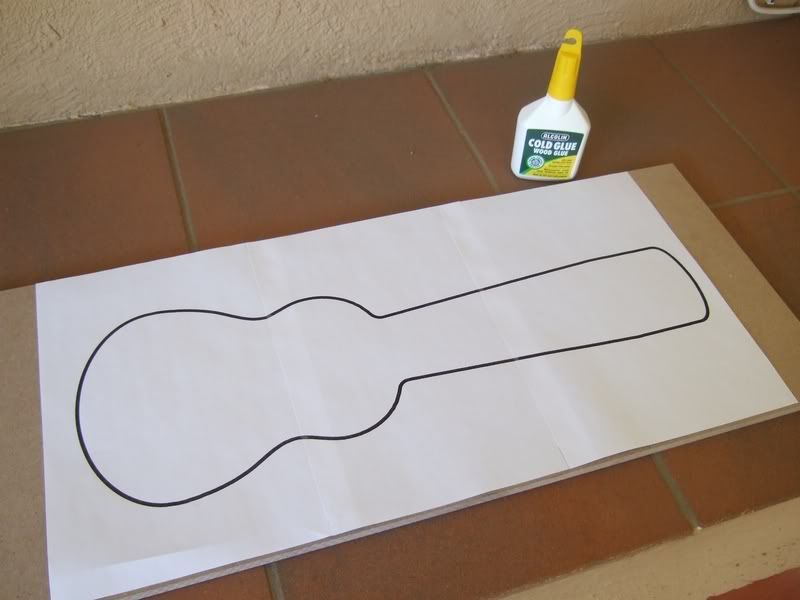
Let's interrupt quickly just to show the bill of materials - at least for the woodworking phase of the project.
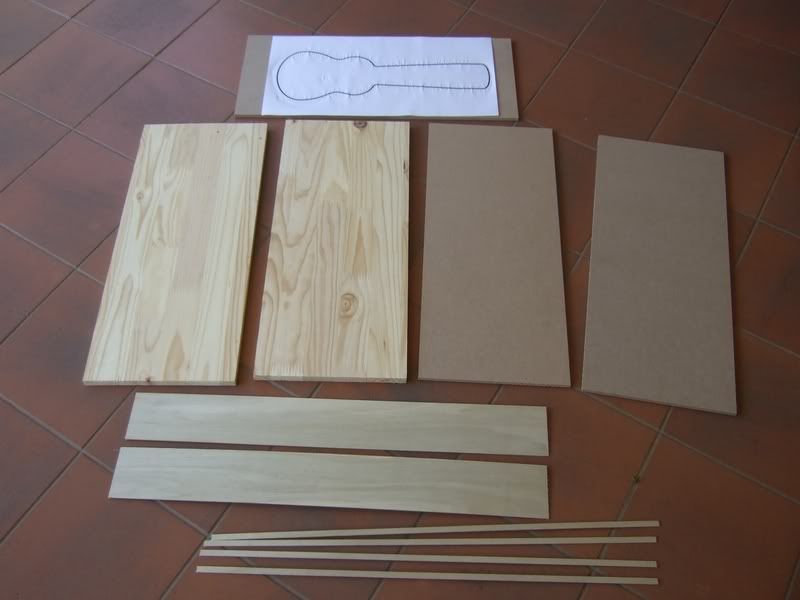
That is:
3 pieces of 9mm supawood, 300x700mm. One to be used for the routing jig and two for the base and top of the case.
2 pieces of 20mm pine, 300x700mm. These will be used as the template to bend the plywood sides.
2 strips of 3mm plywood, 100x800mm. One will be used for the sides of body section of the case and the other on for the neck section.
4 strips of 3mm plywood, 10x800mm. These will be used for the sides of the lid. I think I know how I'm going to do this but it's a vague notion so far and hard to explain. You'll have to wait and see.
OK, so now that the printout is glued onto the supawood, cut it out with a jigsaw.
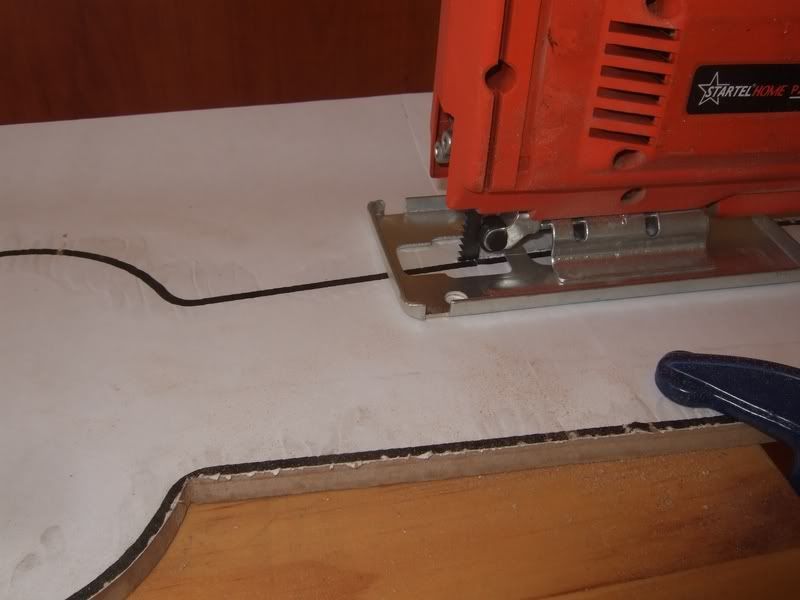
Lessons learned: Rather cut a little bit further from the line. You can always file or sand the wood down to the line but if the jigsaw blade wanders over the line you're pretty much screwed. In Neon Gecko's sage advice: "You can always take wood away but you can never put it back." I was lucky though and only slightly cut into the line in one place. It might not be a big problem but it does bug me a little.
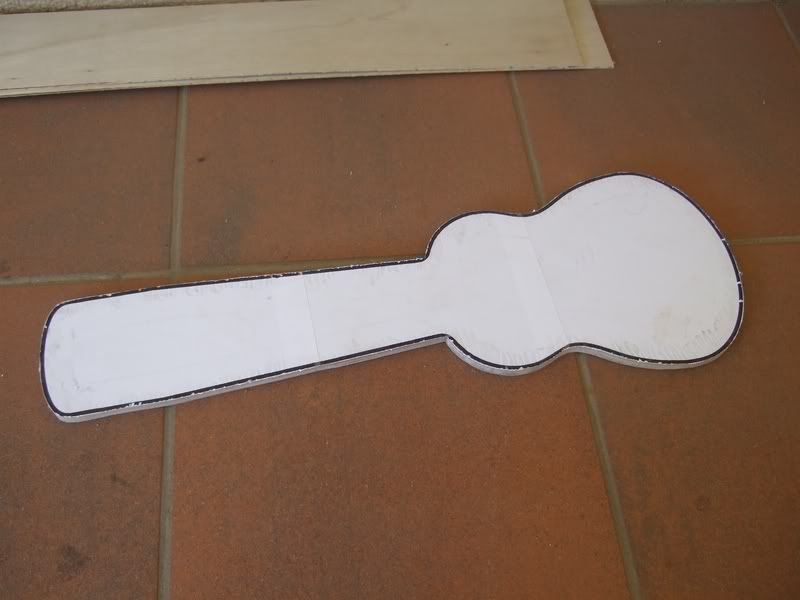
If you look closely, you'll notice that along the side of the neck section, near the tip (in the bottom left of this image) there is a slight concavity to the cut. I didn't even notice this until I started routing around the jig.
OK, so another thing I'd have to make provision for was the fact that my router bit would not be long enough to cut through a 20mm plank of pine. What I did was to sandwich the four planks together and put the template on top, clamp it all together and then drill a few holes through the whole shebang. It is vital that these holes are drilled exactly perpendicular to the planks. A drill press would have been ideal but seeing as I only have a hand held drill I had to eyeball it. I got it fairly accurate but still think I'd have gotten more accurate results using a drill press. The point of drilling these hole is so that I can fit the template to one side of the pine plank, route down to just more than half the thickness of the plank and then fit the template to the back side of the plank and have it line up exactly with the cut made on the front side.
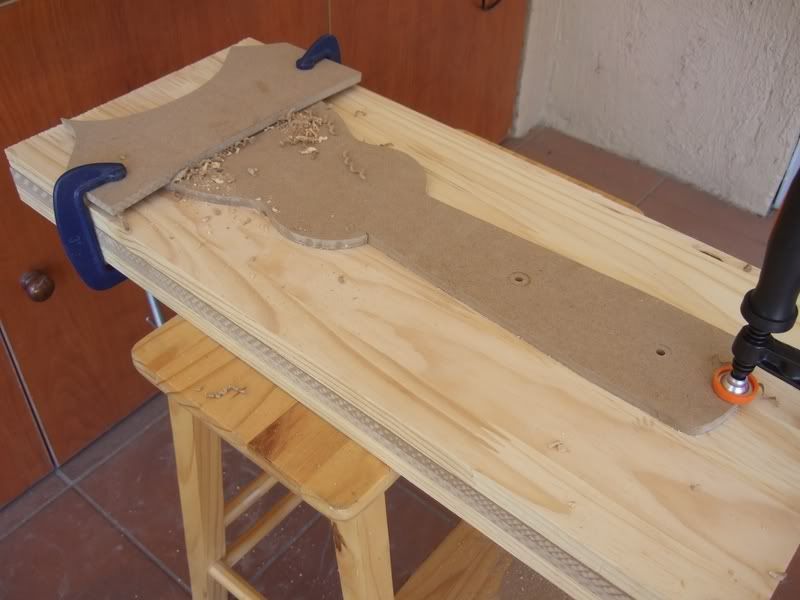
That extra bit of wood on the body side of the template is simply my way of clamping it down. I didn't have clamps that would reach all the way in so I used a piece of off cut supawood and clamped the template down with that.
I then used short dowels of 6mm diameter to fit the template onto the plank to be routed.
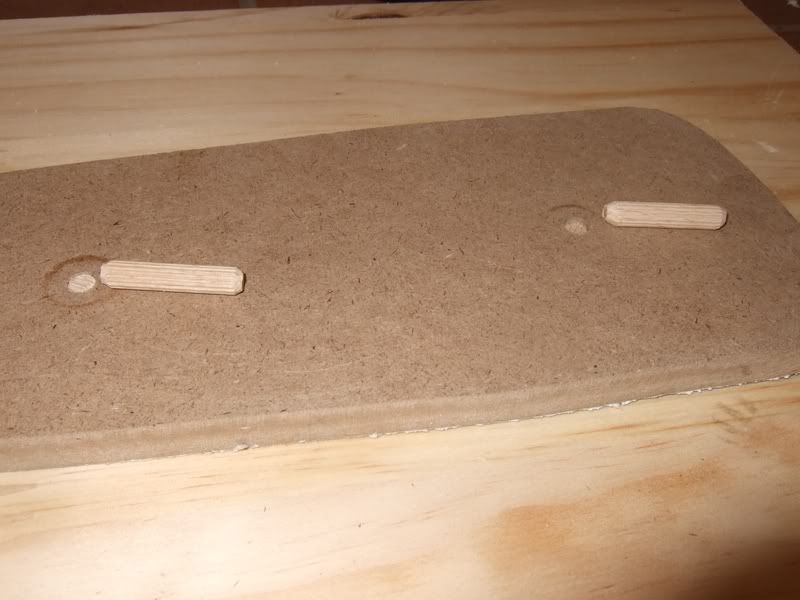
Just important that the dowels don't protrude above the surface of the jig as that would impede the movement of the router sole over the jig.
Now the fun part started. Route along the jig, starting with a shallow cut and progressively cutting deeper. Neon Gecko's rule of thumb seemed to work well that you don't cut deeper than the diameter of the bit. Seeing as I was using a 4mm bit I cut deeper in increments of 4mm.
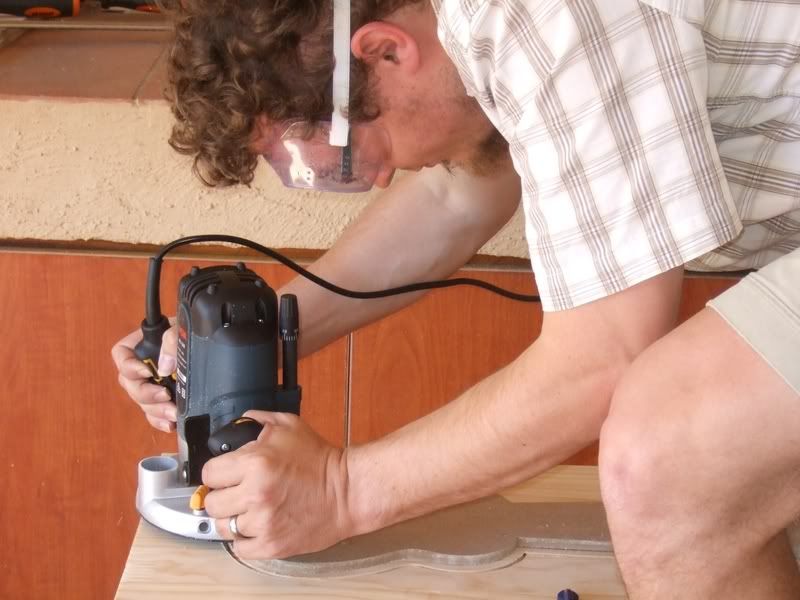
Here is the cut after I reached maximum depth (13mm). After this I flipped the plank around and attached the template again, using the same registration dowels. Notice at the bottom right of the neck section the cut is ever so slightly concave. I'm still hoping this won't affect the end result too badly.
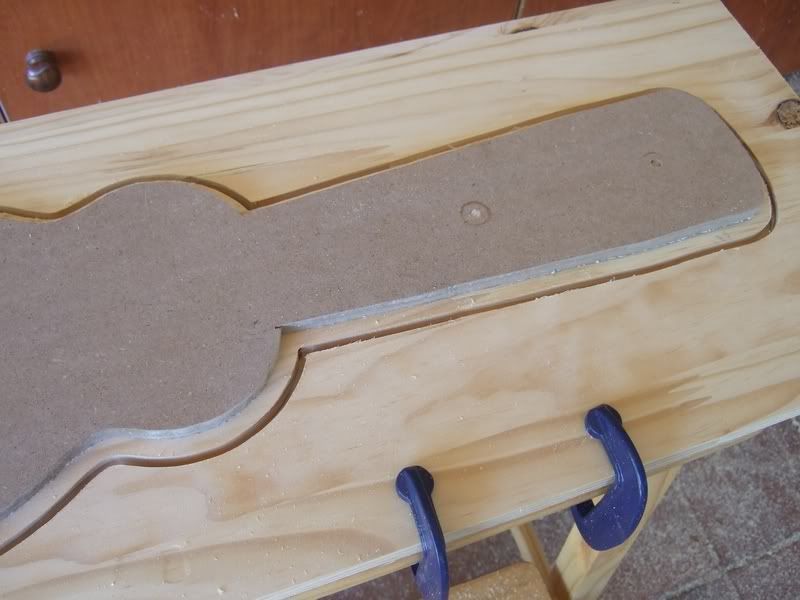
Lesson learned: After finishing a cut, wait for the router to come to a complete standstill before lifting it up. If you don't, you run the risk of breaking your bit. OK, so the whole thing didn't snap in two but I did lose the very tip of the cutting edge which wasn't the biggest disaster but it did mean the the shaft of the bit was now ever so slightly longer than the cutting edge. This meant that consecutive cuts was a bit harder as the shaft would feel the grain of the wood before the cutting edge cuts it. I'll be more careful with future bits but this one did last for all four planks that had to be cut.
Once the cut is made through the plank, rinse and repeat. The second pine plank was cut in exactly the same way and then it was time for the 9mm supawood planks.
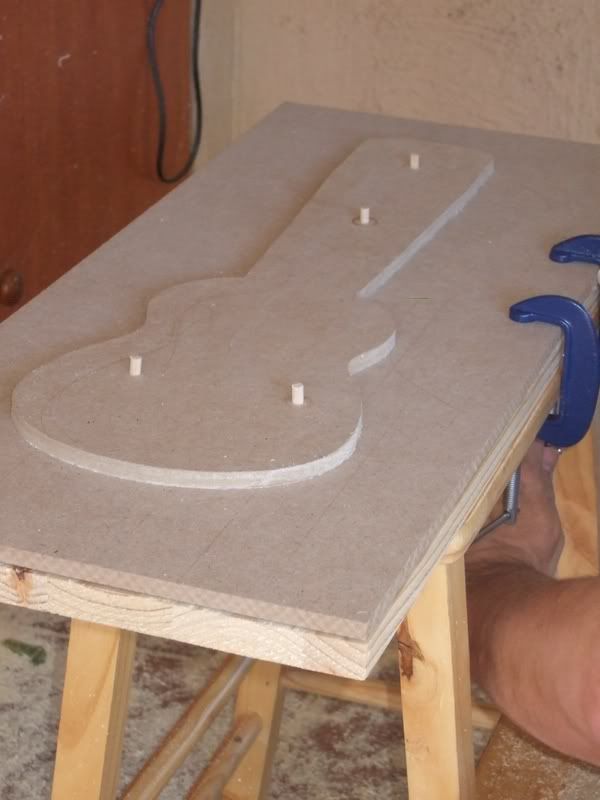
For the two supawood planks the registration holes was probably not required and it would have been more correct, I suppose, to simply clamp the template to the plank and route it without having to drill unsightly holes through the plank. Seeing as the wood will ultimately be covered by vinyl anyway I figured that it wasn't really a problem and I could drill the holes without much reason for concern. Besides, the dowels were a very useful way of fixing the jig to the plank.
And here is the final cut through the 9mm supawood. Of course, it is important to have some other piece of wood underneath the supawood so you don't route into your work surface.
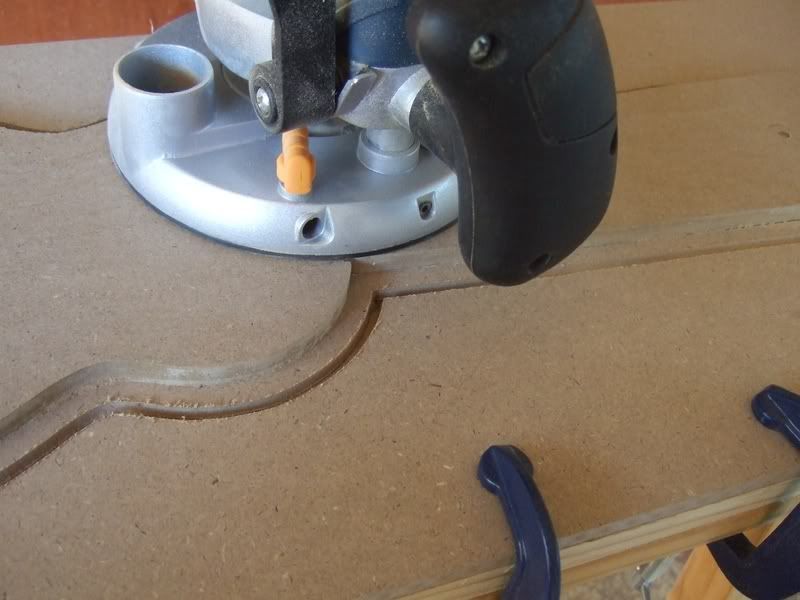
Then, rinse and repeat until you end up with this:
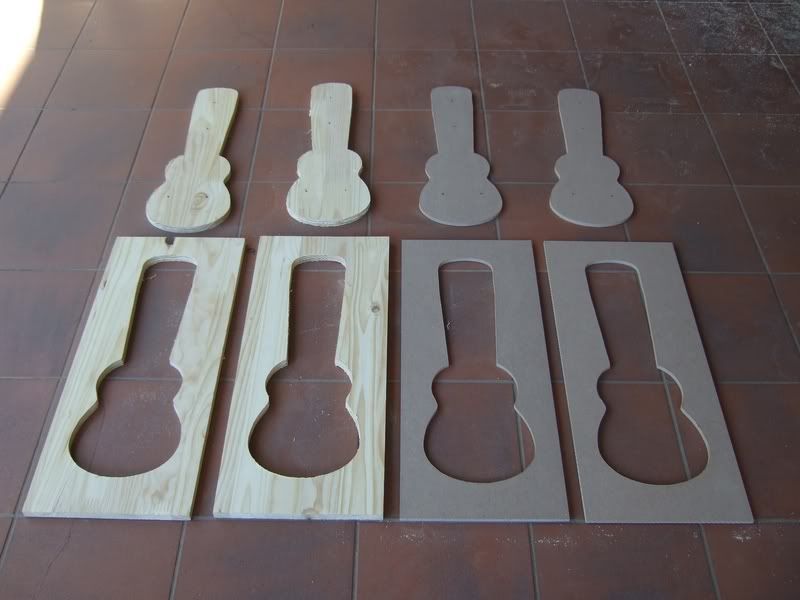
The final step of course is to crack open your hops based beverage of choice as a celebratory libation for making your very first jig-based router cuts. It feels great.
So that's how far I got for now. The next step will be to soak and bend the plywood around these templates. It remains to be seen if the 3mm plywood can actually bend to these curves. I'm particularly concerned about the small curve between the two bulbs of the body but that will have to wait until I get some more time to spend on this.