This nylon string has a nut width of 52 mm, and the nut I received with it had the strings at 45 mm width. The strings felt too close to the edge of the fingerboard, but it played OK. I made up this bone nut, reducing string width to 41 mm, more in line with my other nylon (now also with a bone nut, also with reduced string spacing, from as-received 43 mm to 42 mm), and to test the effect of strings spaced closer together. I first used the old nut off the other guitar to test the playability before I committed to cutting.
This is driving me nuts. Cutting string slots accurately is not that simple, and maybe small (what is acceptable?) variations in spacing between the strings will not be felt, or have an effect on playing, but one wants to do this right. For this one I dialed out the slots on the milling machine. Even milled the Bass E slot with a 1 mm center drill, which proceeded to break as I marked out the rest. I used 1 mm, 0.8 mm and 0.5 mm drill bits to mark the slots and drill holes to slot depth, in the hope that it will simplify the process, but, really, that is too much hassle. The 0.5 mm drill is pushing my luck anyway. I used the 0.8 mm drill as a milling cutter to deepen the A string slot, but the rest I had to resort to my collection of modified saw blades for final shaping. Polishing the slots was done with old guitar strings.
I need to make a slotting tool, with music wire "saw blades", but how to roughen them up sufficiently to cut at a reasonable tempo? Dialing out the slots on the mill is good, I can continue with that. Previously I marked out with the vernier and pencil, and proceeded from there, but I cannot place the saw and cut accurately enough to get it "just right". With guide slots scratched on the milling machine (or "milled" with a pointy burr) that is taken care of.
Correct, the nut is not quite done yet. The slots for the thinner strings (Thomastik-Infelds) are too deep, the convention says slot depth should be half string thickness. Hmm, on an electric with 0.23 mm bottom string, I think not. I shall play and test for a while, adjust (sand bottom of nut) final string height, and then sand off at the top to neaten it up. But I cannot imagine myself sanding off the top to go to half the bottom E thickness, that will leave a slot 0.2 mm deep. Be realistic.
This took too much time, I need to streamline the system.
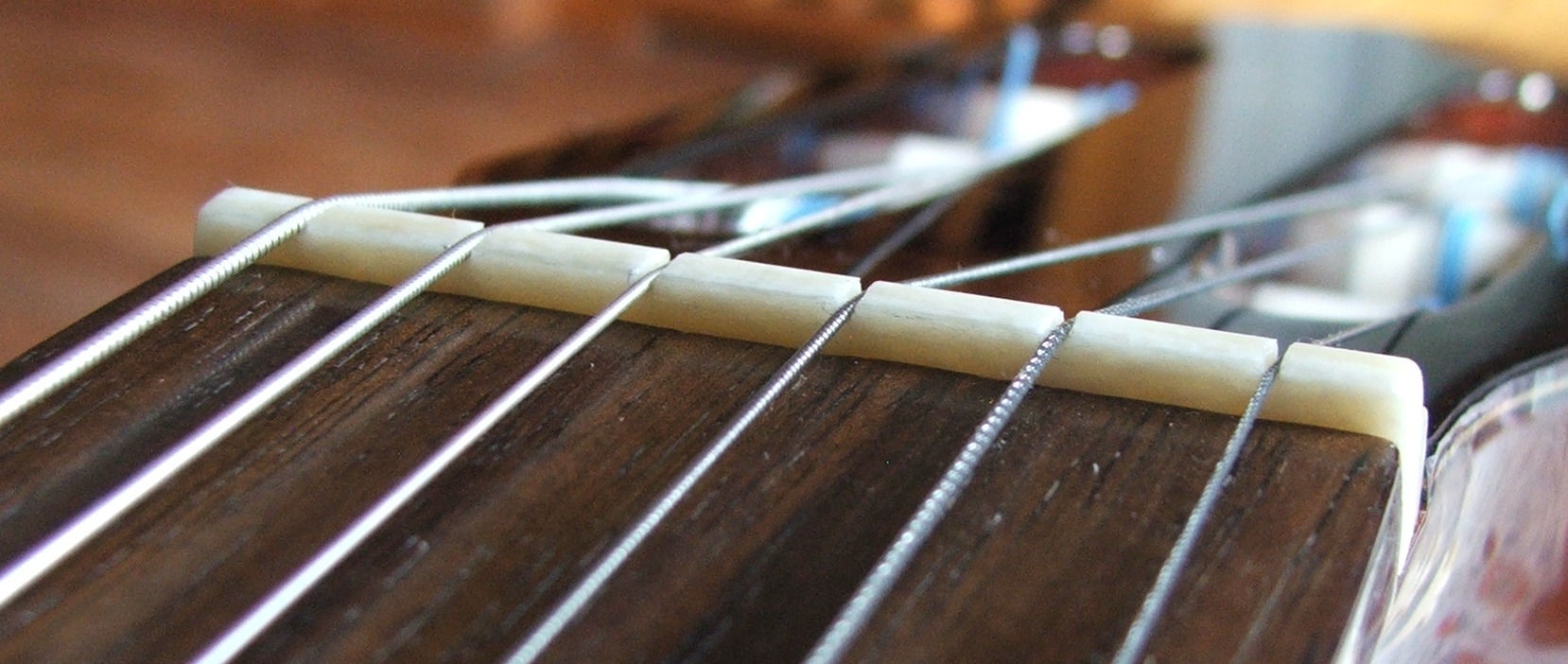
Nuts and bones of setup
a month later
The quest for perfection continues. I decided that I should rather try wider string spacing, and made up another nut, streamlining the process, but still without decent nut files. I widened the spacing to about 42.5 mm, and the guitar plays well with that.
The next item would, of course, be a bone saddle. The improvement is arguable, since the saddle rests on a piezo strip, and not on the bridge itself. I made up one from Eland bone picked up in the veld, the bone having been exposed to the weather for at least four months. It is hard, but will flake off easily. Started to go "off" already. I made up the saddle to duplicate the original's (the notched one in the photo) string height. Playing indicated lack of, well, imagination. A "dull" sound, without the "ping" to the trebles. Whether this is due to the material I cannot say, but I measured the action to be in the steel string category, which might be too low. The guitar has a smaller body depth than what is found in "pure" acoustics, and that does influence the sound, but the sound with this saddle was unacceptable.
I made up another bone saddle from the same cow bone as used on the nut, this being much fresher, as well as a bit "underdeveloped", bone density-wise. I lifted the action back to the Low end of nylon string settings, in this case about 0.7 mm. I also increased the saddle thickness, to be a better fit in the bridge.
With the higher strings (and increased break-over angle and increased leverage on the top, etc.) the guitar has a stronger sound, the strings "sing" and the tone is "full". Much more pleasing, but the action is noticeably harder. Playability suffers, but then, if the instrument does not satisfy acoustically, why play? We all know this thing is full of compromises. I shall try it for a while, and see if I shave off the saddle by 0.5 mm or so.
Interesting thing, this guitar, stringed with Thomastik-Infeld Classic S KR116 rope cores, has good intonation at fret 12, only 3 - 4 cent flat. I suspected lifting the saddle will sharpen that, it does, slightly, but still not bad. They did a good job on designing these strings. Seems the 6th string goes slightly sharp now, but making up a saddle with offsets dedicated to this set of strings is futile, I am not planning to make up a saddle for every set I fit, unless I change to another type of string.
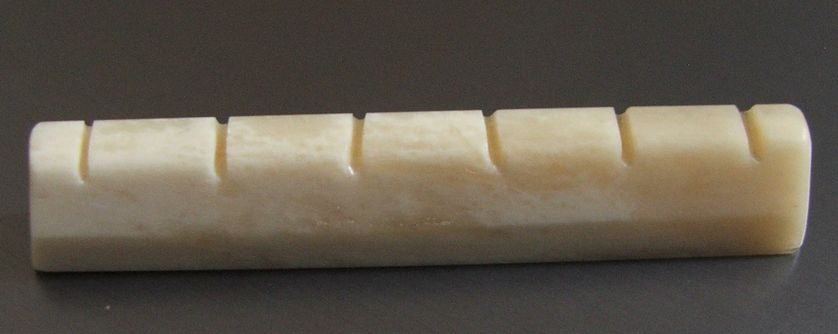
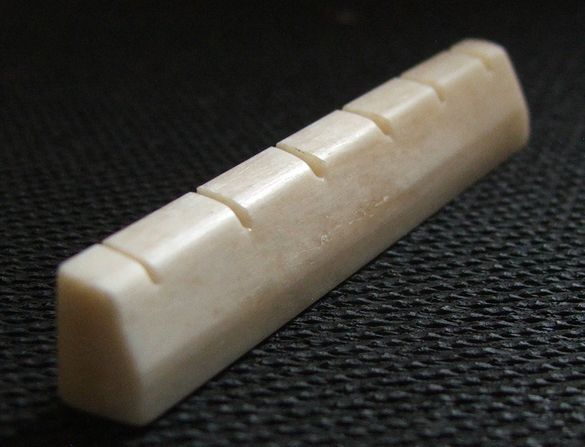
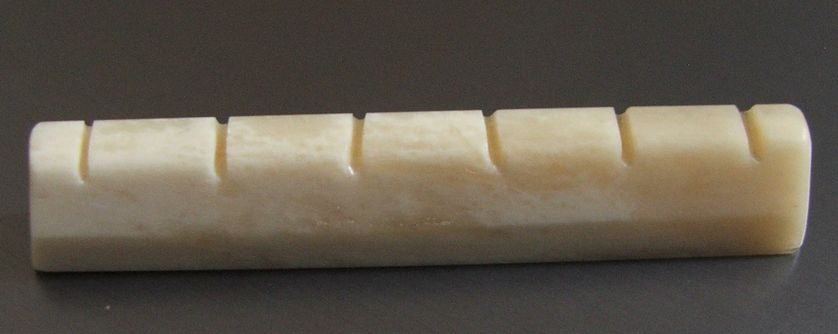
The quest for perfection continues. I decided that I should rather try wider string spacing, and made up another nut, streamlining the process, but still without decent nut files. I widened the spacing to about 42.5 mm, and the guitar plays well with that.
The next item would, of course, be a bone saddle. The improvement is arguable, since the saddle rests on a piezo strip, and not on the bridge itself. I made up one from Eland bone picked up in the veld, the bone having been exposed to the weather for at least four months. It is hard, but will flake off easily. Started to go "off" already. I made up the saddle to duplicate the original's (the notched one in the photo) string height. Playing indicated lack of, well, imagination. A "dull" sound, without the "ping" to the trebles. Whether this is due to the material I cannot say, but I measured the action to be in the steel string category, which might be too low. The guitar has a smaller body depth than what is found in "pure" acoustics, and that does influence the sound, but the sound with this saddle was unacceptable.
I made up another bone saddle from the same cow bone as used on the nut, this being much fresher, as well as a bit "underdeveloped", bone density-wise. I lifted the action back to the Low end of nylon string settings, in this case about 0.7 mm. I also increased the saddle thickness, to be a better fit in the bridge.
With the higher strings (and increased break-over angle and increased leverage on the top, etc.) the guitar has a stronger sound, the strings "sing" and the tone is "full". Much more pleasing, but the action is noticeably harder. Playability suffers, but then, if the instrument does not satisfy acoustically, why play? We all know this thing is full of compromises. I shall try it for a while, and see if I shave off the saddle by 0.5 mm or so.
Interesting thing, this guitar, stringed with Thomastik-Infeld Classic S KR116 rope cores, has good intonation at fret 12, only 3 - 4 cent flat. I suspected lifting the saddle will sharpen that, it does, slightly, but still not bad. They did a good job on designing these strings. Seems the 6th string goes slightly sharp now, but making up a saddle with offsets dedicated to this set of strings is futile, I am not planning to make up a saddle for every set I fit, unless I change to another type of string.
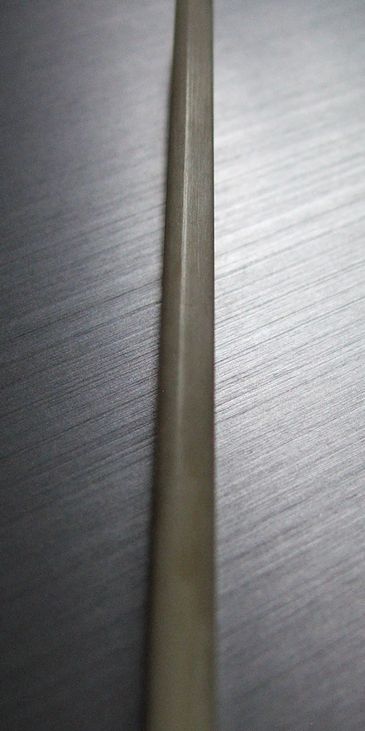
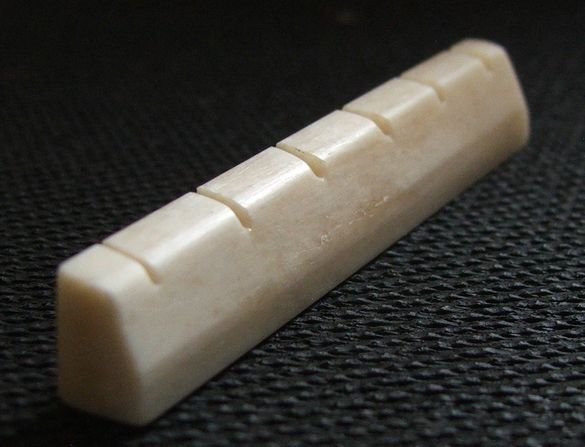
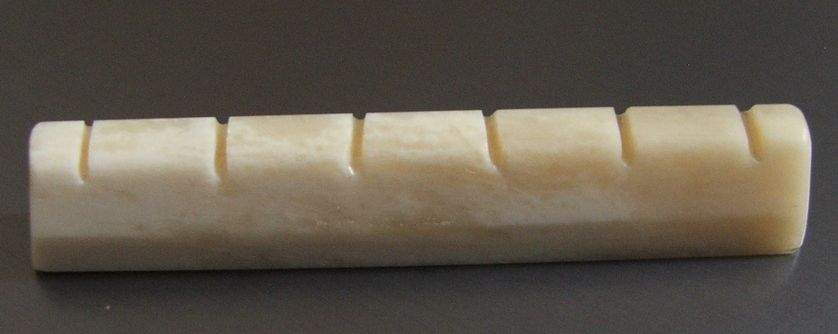
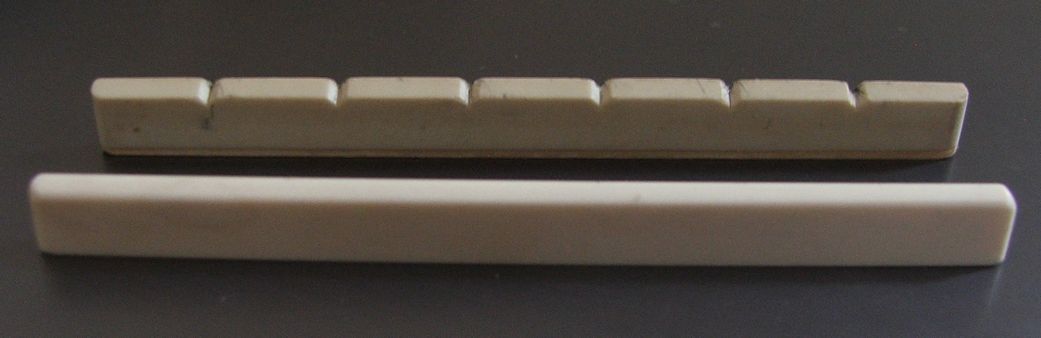
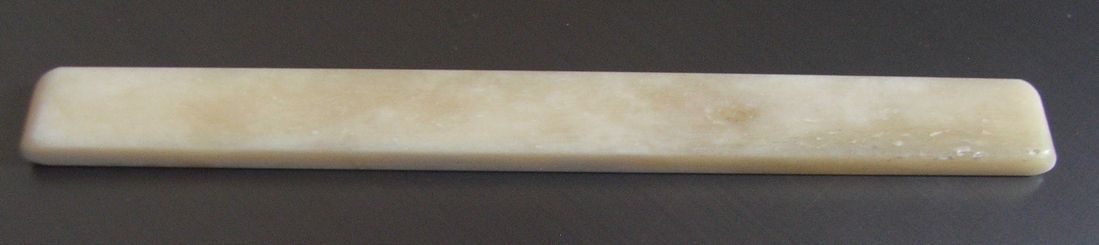
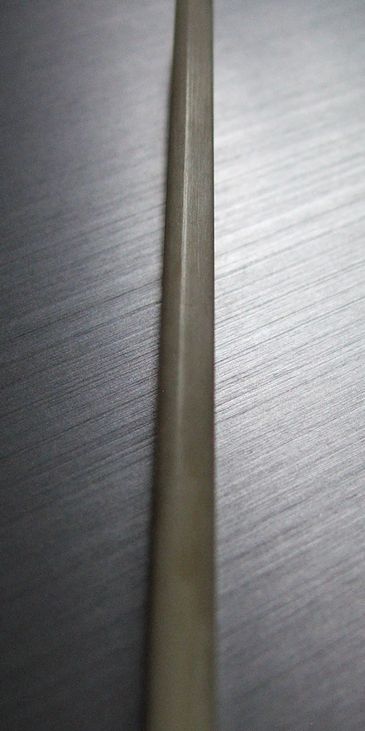